Packaging Line
Setting up an automated packaging production line can bring a range of benefits to your operations, including increased production speed and implementation of more effective control measures, while lowering labor costs and making a safer working environment for employees. When you’re beginning the process of implementing packaging automation, determining your needs and planning carefully is crucial. From planning workflows to creating new production goals, we will guide you through the entire process and ensure you obtain the ideal solution for your needs. We will introduce some initial considerations for setting up an automated packaging line.
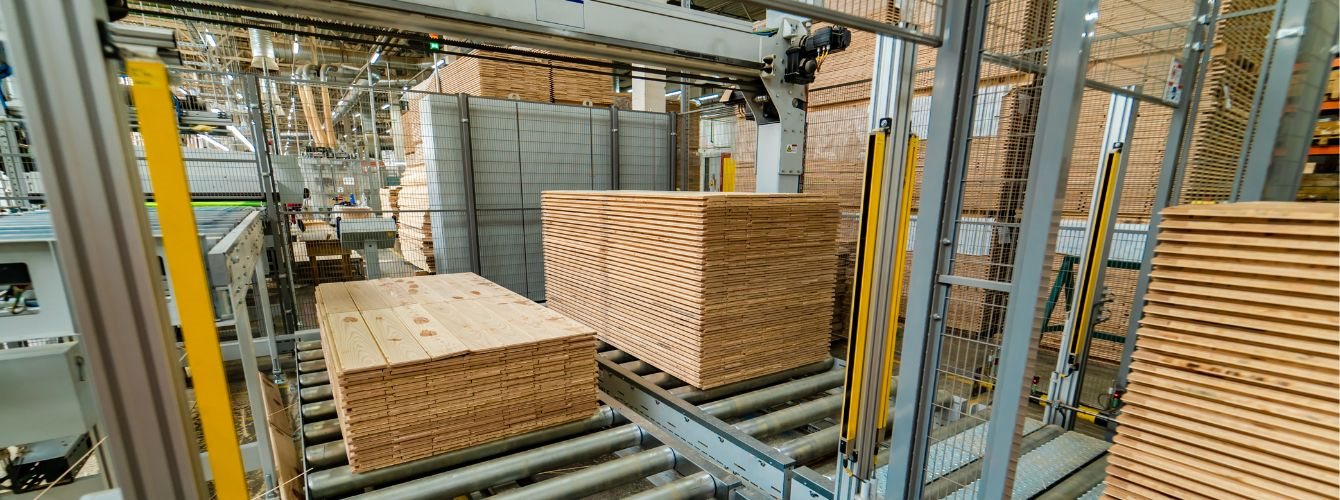
Your goals
-
Think about your long-term production goals
Establish the desired production volume for the automated packaging line. This will help to determine the size and capacity of the equipment required and the number of workers required to operate the line, which will affect your production goals.
-
Cost
Establish a budget for an automated packaging line and taking into the cost of equipment, labor, materials and maintenance. Also consider the desired speed of the production line. Higher speeds can increase efficiency and productivity but may require more advanced and expensive equipment.
-
Package types
Identify the packaging required for the product. This will help in choosing the appropriate packaging equipment and materials.
-
Flexibility
Consider the possibility of packaging different products in the future.
Conduct the equipment assessment
-
Environment / Space availability
One of the primary factors in determining your approach for packaging line automation is to take a look at your existing factory environment. Define the available space for the production line, including the facility's size and layout, as well as any potential expansion options as the business grows. The design of the production line layout should optimize space and ensure an efficient workflow. To figure out if you have enough space in your factory to install an automated packaging machine or packaging line, you will have to take note of the size of the equipment you will need and determine whether your factory space can accommodate the actual footprint of the new equipment.
-
Labor force
Determine the number of workers and any training that may be required to operate the new production line.
-
Power requirement
Assess the power requirement of the production line, including electrical power, air compressed, and other utility requirements. This will help to establish the cost of installation and operation.
-
Maintenance and Support
Evaluate the equipment’s maintenance and support capabilities. This includes the availability of equipment maintenance personnel and source spare & replacement parts and the ability to support with maintaining the equipment over time.
Implement quality control
-
Installation
Before installing automated packaging equipment, the factory's infrastructure must meet the equipment requirements, include power supply, space and environmental conditions. This involves simulating operations in an actual production environment to check for any errors in the automated packaging line process.
-
Training
Provide training for the workforce on the operation and troubleshooting.
-
Define quality standards
Clearly define the quality standards for the package, such as product packaging safety. For example: package each product individually, to put them in a carton, there are carton sealing machines to proceed tape sealing.
Deciding to invest in new equipment is a big decision for any business. Any whether you are moving from a fully manual process or semi-automated process, introducing automation to your packaging line can bring a range of benefits to your operation.
To learn more about automated packaging line solutions get in touch We are always more than happy to help.